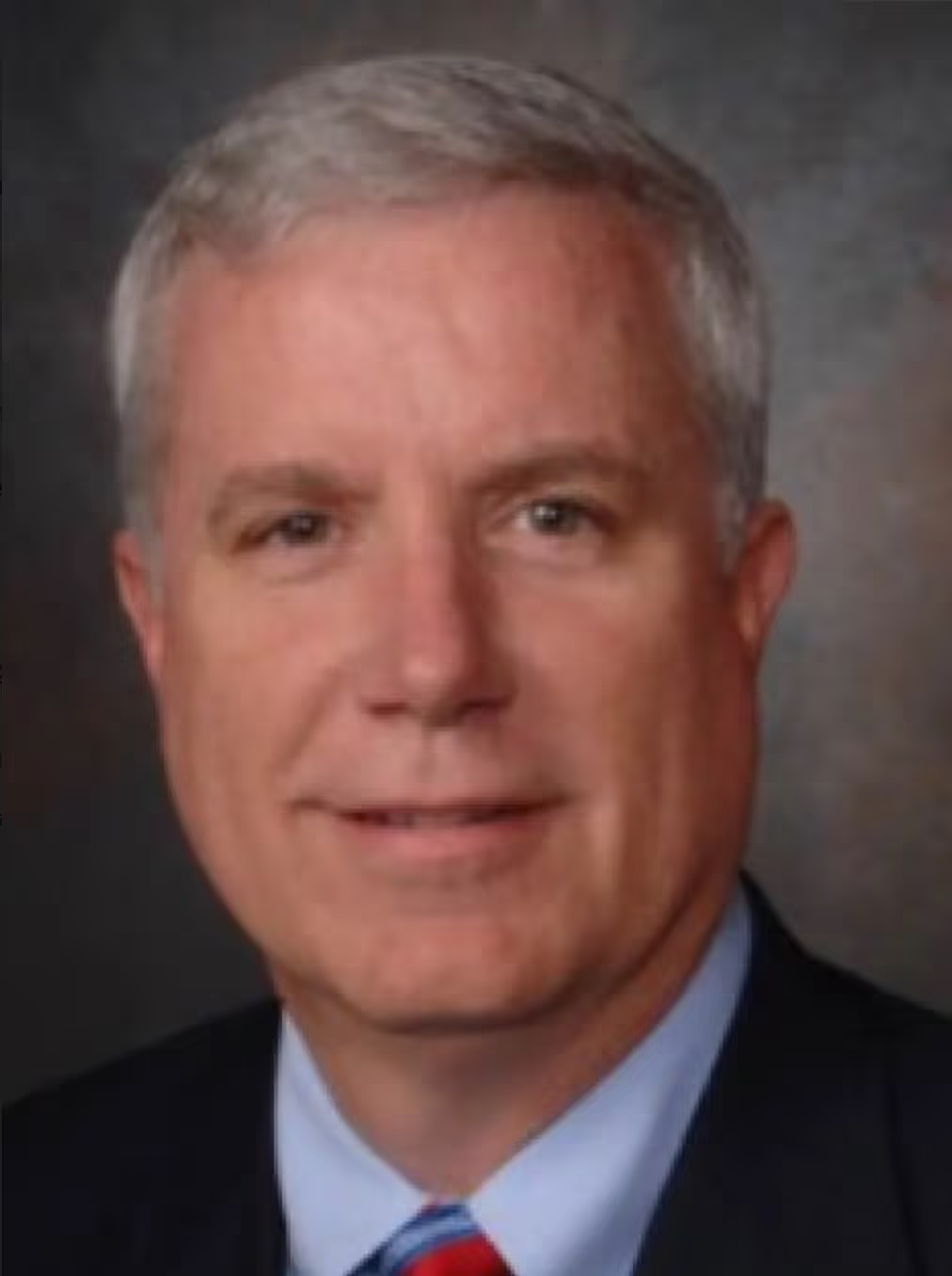
The Story
10 years ago, Premier Service Co. was struggling to keep their Field team focused on building. Instead, they were spending their time worrying about which materials had been ordered and dealing with deliveries to the job site. To solve the issue, they decided to add warehouses to their business operations. “We moved to warehouse space and made sure that our employees in the field were not burdened with needing to know about what was coming in, unloading materials, and all that kind of stuff,'' says President Gary Phillips. However, having a warehouse but lacking visibility into what was in stock was creating more pain for Premier than they wanted.
They needed a way to stay informed on what materials were available in the warehouse and although the Warehouse team worked within their office, Field teams were still in the dark. Without knowing what was ordered and when it would be shipped to the job site, the foremen couldn’t properly plan their days and resorted to creating orders for materials that were already sitting in the warehouse.
Over the next decade, Premier tried different methods to fix their warehouse problem with no success. From using cumbersome pen and paper to spreadsheets that required tedious data entry, to building expensive custom software, nothing was working. Gary explains, “Spreadsheets don’t tie in the [Purchase Order] side so you have to write a PO, and then you have to write it again for purchasing and then go back and manually update when you receive materials. It just didn’t work.” They needed a solution to know which materials were in the warehouse at any given time.
The Solution
Kojo Warehouse provided the ideal visibility for Premier. With the help of Kojo’s Customer Success team, Premier easily adopted and implemented Kojo. Instead of ordering duplicate materials at the jobsite, Field teams could now see and request what's in the warehouse from their Kojo mobile app, ultimately reducing the amount of leftover materials.
By gaining real-time visibility of what's coming in and out of the warehouse, Premier's purchasing team is:
- Making smarter purchasing decisions
- Taking advantage of using more of the materials readily available in the warehouse
- Purchasing less to reduce waste
- Cutting down on on job delays
- Increased bulk ordering
- Reducing material costs
Gary explains, “I’d estimate as close to 60-70% of our material buys are now done in large quantities and over multiple jobs at a time because we can now see what we bought for each individual job.” Premier has now solved their 10-year challenge of bringing visibility into warehouse inventory for their field, office, and warehouse teams.
Their Favorite Features
- Warehouse material tracking
- Real-time view into inventory
- Digital requisitions and POs
- Delivering tracking
- Job costing
Read More
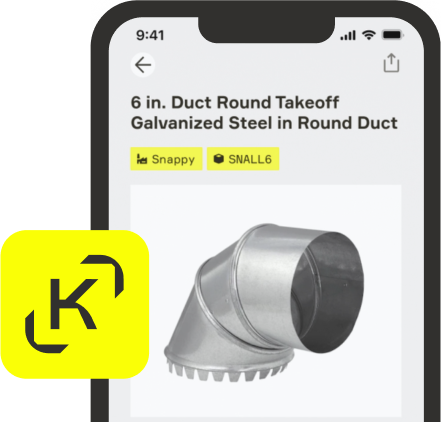