Centralized Inventory Management with Multi-Warehouse Locations
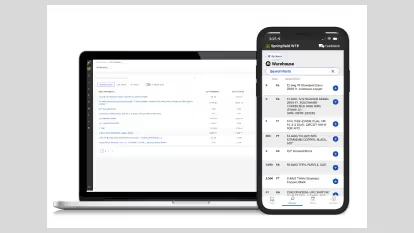
If you are like many contractors, you face challenges with your field teams knowing what you have sitting in your warehouse. This problem compounds when you have more than one inventory locations.
Kojo is here to help. We are excited to announce our new multi-warehouse location feature as part of our Warehouse module. This feature allows you to manage and track inventory across different physical locations with ease.
We understand that managing inventory efficiently and accurately is crucial to the success of your business. It can be hard for the field crew to know what is available where. With this new blog, you now have even more control and visibility over your inventory, helping you streamline your operations and save time and money.
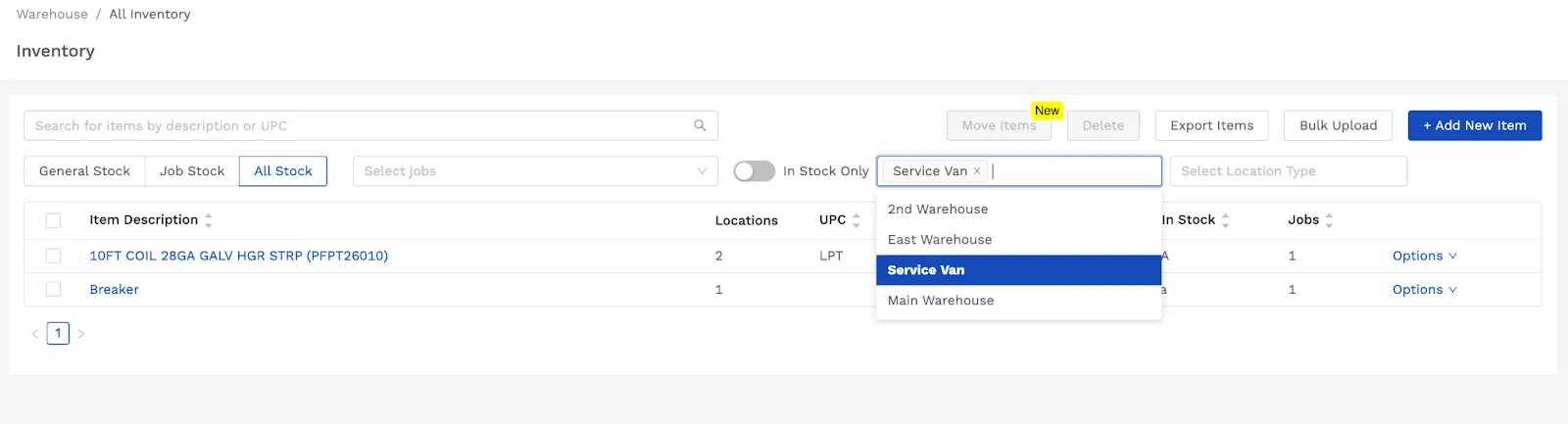
Centralized Inventory Management for All your Storage Locations
As a trade contractor, you may have multiple locations where you store your inventory, such as different job sites, warehouses in different geographical locations, yards, or trucks. With Kojo’s multi-warehouse location feature, you can easily manage inventory across all these locations from a single, centralized platform. Easily sort by any location and view inventory counts across all locations. You can even choose how to fulfill field requests to route them to different locations to optimize your operations.
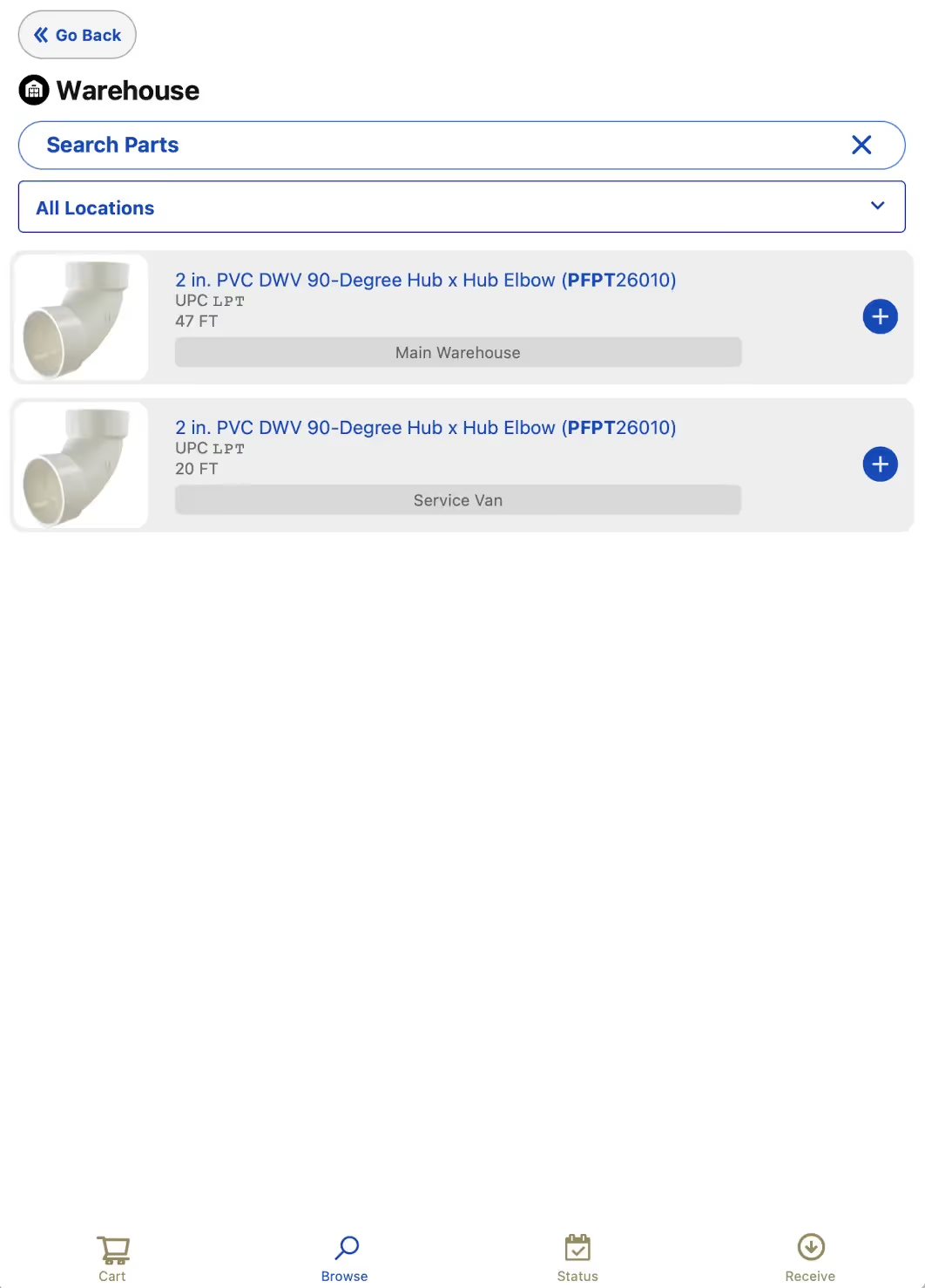
Improve Inventory Visibility Across Geographically Dispersed Locations
Whether your locations are feet or hours away, you can now setup locations how you need. You can control warehouse visibility to ensure only the right users and jobs see your locations.
Leverage Virtual Locations for Custom Needs
Maybe you operate your logistics with a staging location or a will-call area within your warehouse. You can now setup virtual locations like these to create a workflow that supports your specific business needs rather than other Warehouse Management Solutions on the market that are focused on retail management.
Advanced Visibility, Stock Level, and Inventory Management Tools
You can track the quantity and location of each item in real-time, transfer inventory between warehouses, and monitor stock levels to ensure you have the right items in the right locations at the right time. This helps you maintain inventory levels and prevent costly delays to your projects.
Job Container Flexibility and Theft Reduction
Now you can allow your field crew to track and manage their inventory in connexes stored onsite. Field members can easily request replenishment of material from your main warehouse and with a few taps pull inventory out of the container’s inventory. With this improved visibility, you can now better track material usage on the job site and help prevent material theft.
Improved visibility of your warehousing locations means improved project execution for your team. Complete your projects on time by giving your team access to what you have in stock with Kojo Warehouse.
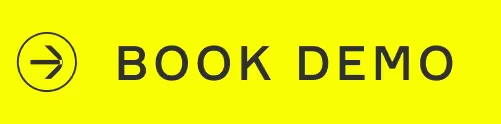
To see how this works, schedule a demo with Kojo today.
Related posts
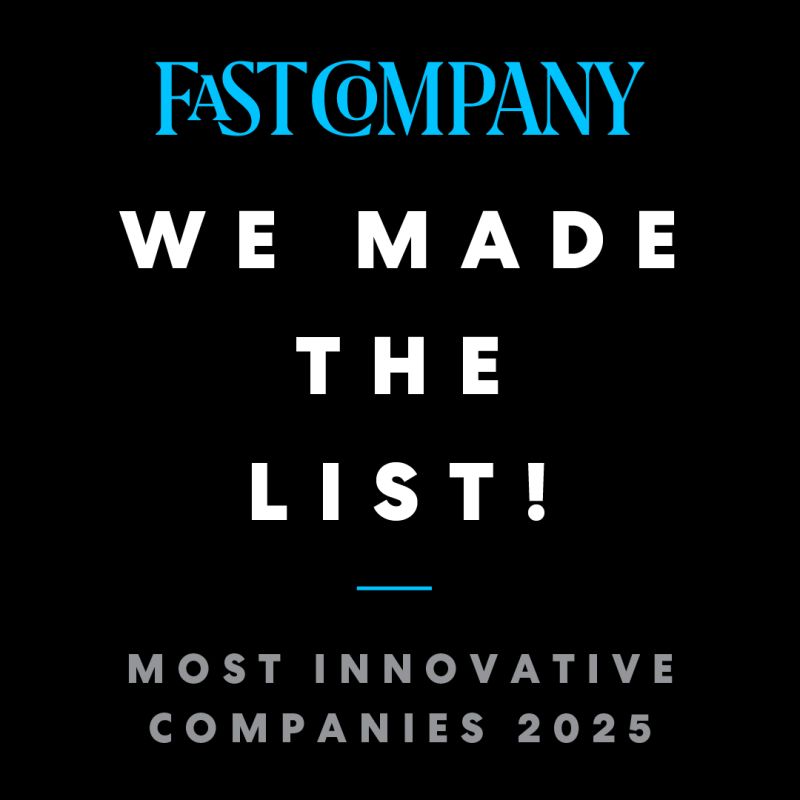
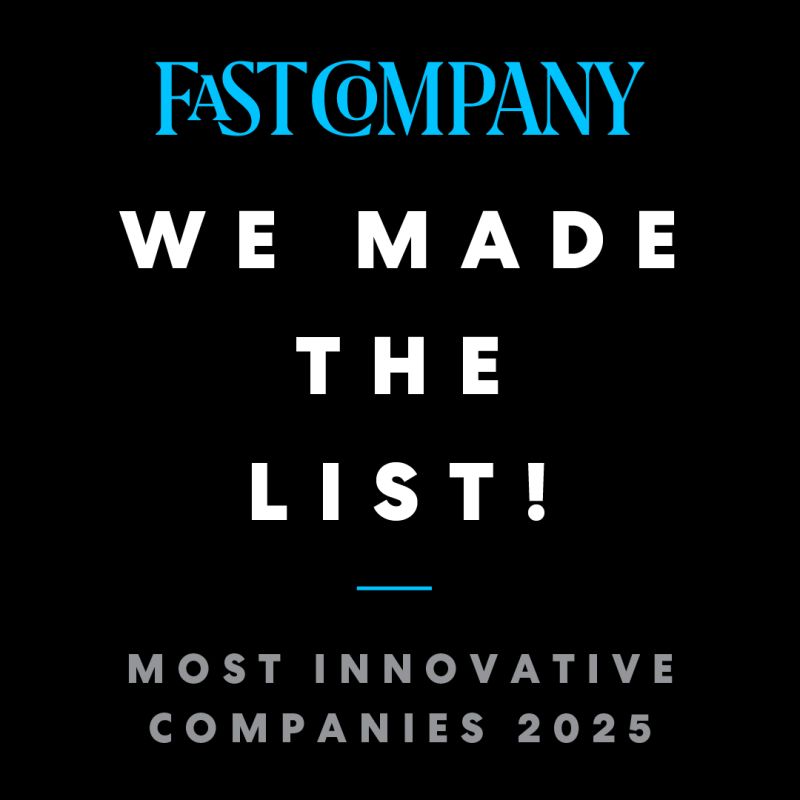
Kojo Named One of Fast Company’s Most Innovative Logistics Companies of 2025
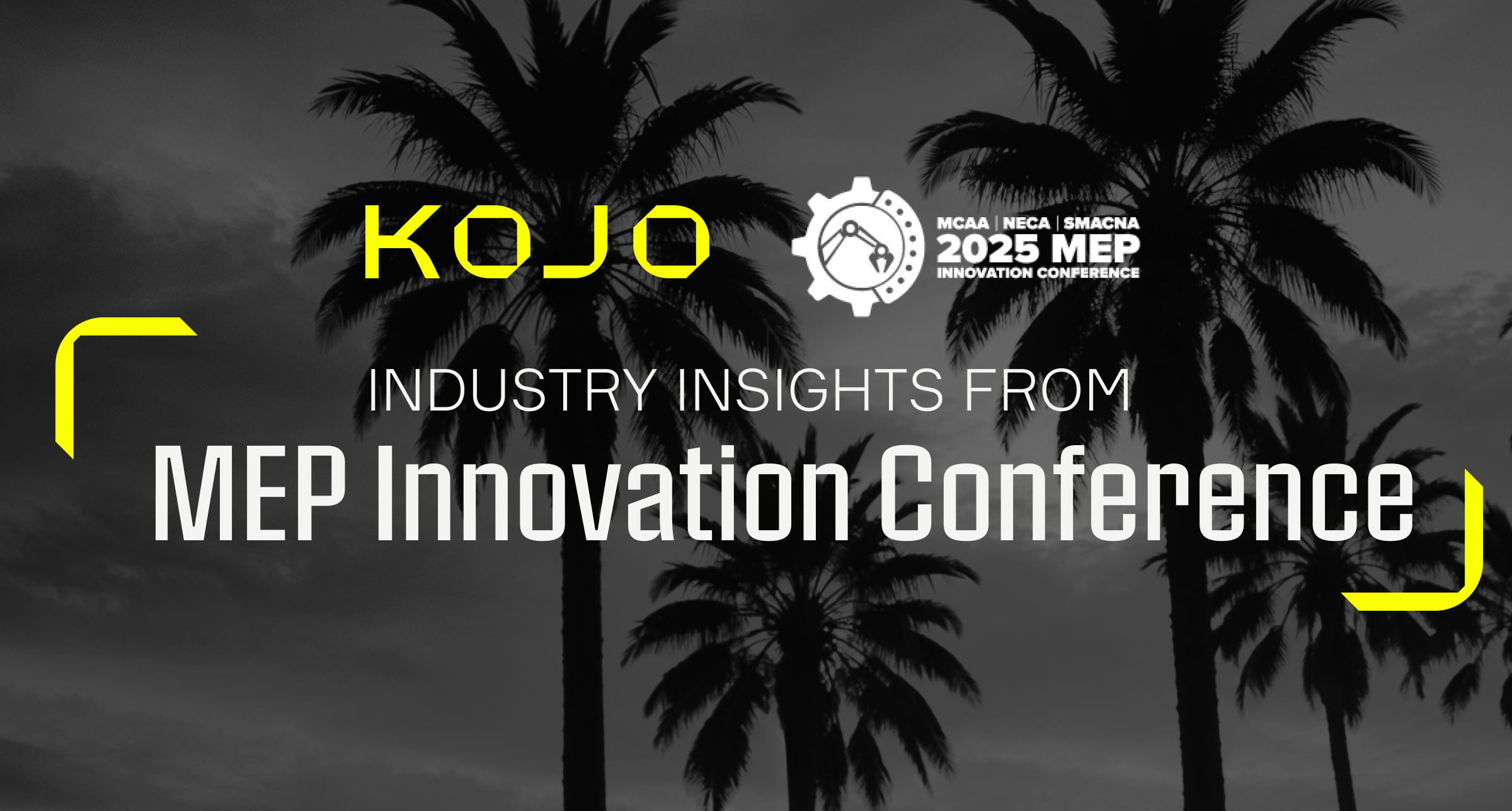
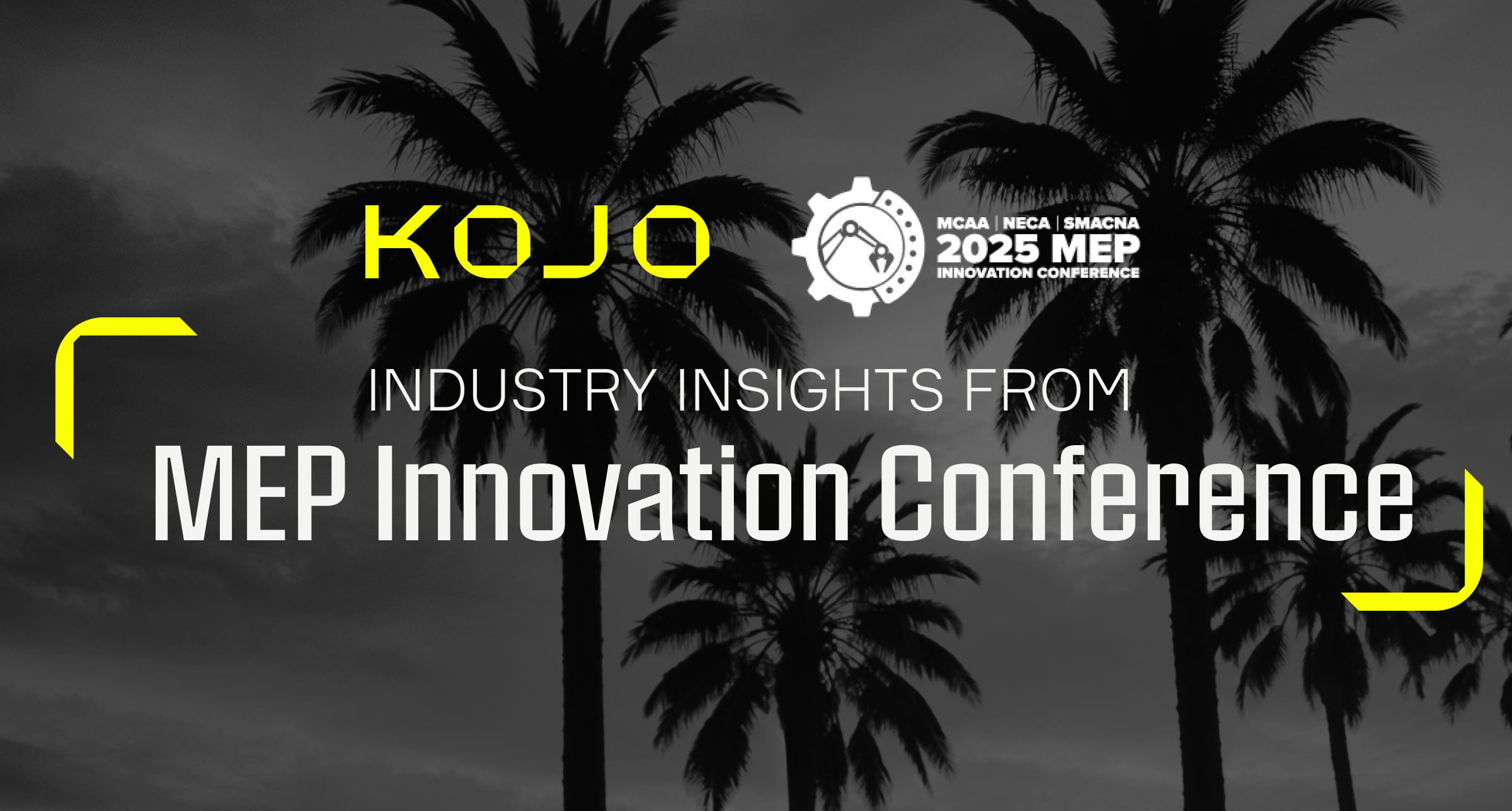
Industry Insights From MEP Innovation 2025: Trends We Observed
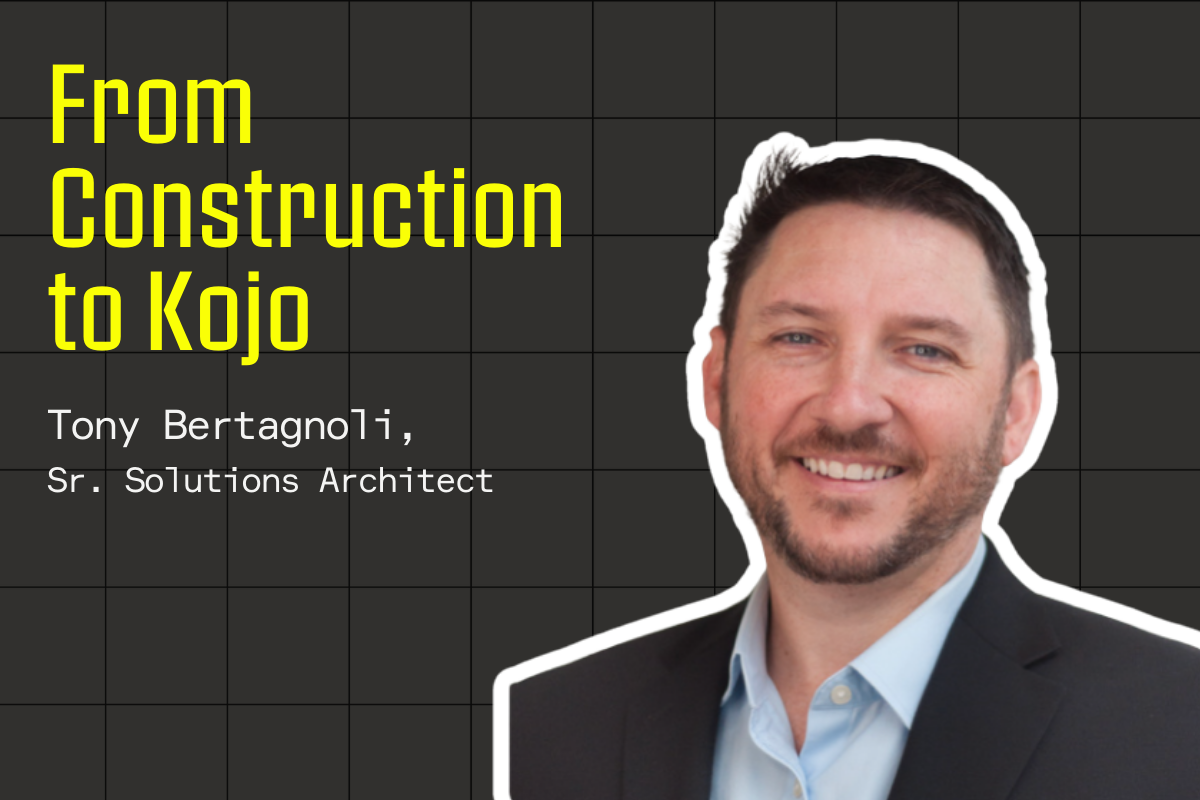
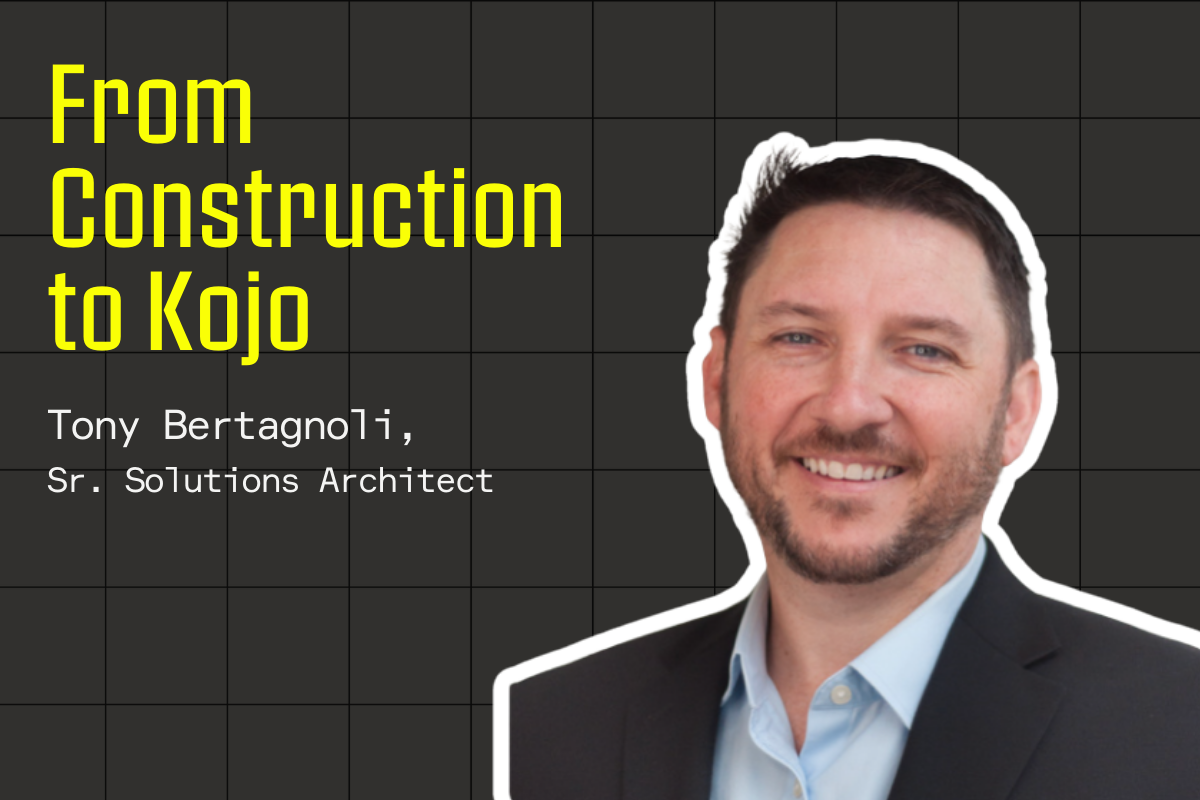